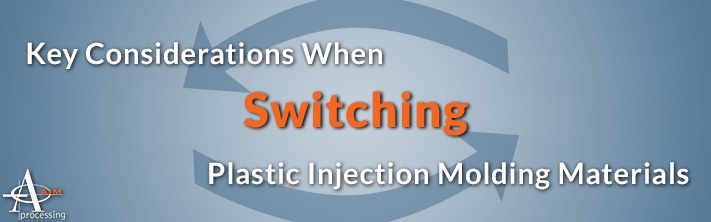
You’ve designed your part, created the tooling, and are ready to begin the plastic injection molding process. But then, there is a change of plans. Rather than using ABS plastic, you will now be making the parts out of nylon. No problem. Just have some nylon shipped to the manufacturer and you’re good to go, right?
Maybe … but more likely not. It has long been advised that you shouldn’t “change horses in midstream.” The same could be said of switching materials just prior to starting production. If you must, there are some considerations you should keep in mind.
What You Need to Know About Switching Materials
To ensure that your plastic injection molding project produces small plastic parts that meet your requirements, be sure that you, your designer, and your manufacturer all consider these issues if you decide to switch materials:
- Shrink rates. Different materials have different shrink rates. For example, ABS and Polycarbonate shrink in the range of 0.004” – 0.006” per inch. Nylon and acetal, on the other hand, can shrink 0.022” – 0.030” per inch. Consequently, switching from, say, PC to acetal will give you a significantly smaller part. In some cases, that may not pose a problem. However, if the now-smaller part is just one component in an assembly, and the others are still being made from PC, the pieces may not fit together properly. This can also be the case with components that don’t shrink at all such as metal clips, circuit boards, or lenses.
- Material-specific gates and vents. Gates and vents are sized for a specific type of plastic. Changing from one material to another can cause flash problems if the gates are appropriate for ABS but the wrong size for nylon, for example. Other issues can arise as well. Burns can occur if the nylon gates are too small for ABS, parts may exhibit blush if the gates are too small because you have switched between two materials that flow differently, etc.
- Additives. People often think that the last-minute addition of something like fiberglass to increase the stiffness of the finished product won’t affect the manufacturing process. However, fiberglass will significantly reduce the shrink rate of a part. Fiberglass is also very abrasive on the tool, so if the tool is not made of a hardened or wear-resistant material, its life will be cut short.
Bottom line: You should only change materials if you are fully aware of the impact the change will have on the part, associated parts, and your tooling.
Helping You Survive the Switch
In some cases, switching materials is unavoidable. That’s when the knowledge and experience of your plastic injection molding shop really comes in handy. At AIM, we’ve been in business for more than two decades and have both an in-depth understanding of how material changes will impact a process and, in many cases, workarounds that will allow you to make the switch without producing a negative impact on your project.
To learn more about our services, contact us today or stop by our facility in Longmont, Colorado, just north of Denver. We’re happy to answer any questions you have about our shop or your small plastic part injection molding needs.
