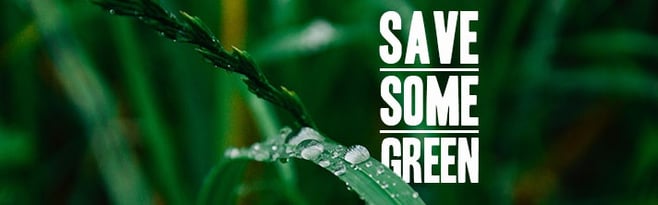
Plastic injection molding is a very cost-effective way to produce high-quality parts. Even so, there are a number of things you can do to save even more money on a project without sacrificing anything in the finished product.
Use designs that minimize materials. Features like ribs and gussets can make a part stronger while using less material. Even a small reduction multiplied by the many parts in a production run and potentially many production runs can add up to big savings.
Ensure adequate draft. In injection molding, as in all manufacturing processes, time is money. Parts that have the appropriate amount of draft allow faster ejection from the mold and save precious seconds.
Consider mold longevity in your design. Anticipating how long your project is expected to be in production will help you build the mold that is best matched to the task. This will minimize unnecessary expenses at the beginning of your project or costly surprises later.
Use materials that meet—but don’t grossly exceed—your needs. While it’s critical that your raw materials meet your requirements, using resins that go far above them or have qualities unnecessary to your project, is simply wasting money. Don’t skimp, but don’t splurge. Explain to your material provider what you are trying to accomplish but also let them know that you want to do so economically.
Produce as many parts at a time as possible. Spreading setup costs over a large number of parts results in a lower cost-per-piece.
Minimize secondary processes. Secondary processes, like ultrasonic welding, pad printing, or painting, are necessary in some cases. But sometimes, a secondary process such as machining can be eliminated by creating an assembly feature within your tooling.
Choose the right shop. Plastic injection molders tend to have specific areas of expertise. Finding one whose specialty meets your needs ensures that you won’t be paying more to have a molder modify its processes to accommodate your requirements.
The more money you can save on producing your plastic parts (without cutting corners, of course), the more competitively you can price your finished product. Use the tips above to give your company the edge.